ProGrid® Compo GC Asphalt Geogrid Composite: The ideal solution for crack mitigation & improving asphalt fatigue
Project: Pacific Motorway M1 North Upgrade
Date: April 2020 to mid 2021
Location: Pacific Motorway M1 Northbound, Sports Drive to Gateway Motorway
Product: Over 80,000 m2 of Progrid® Compo GC 50/50 Asphalt Geogrid Composite
Project background
In 2021, the Queensland Department of Transport and Main Roads (TMR) completed construction on a major upgrade to a 3.5-kilometre section of the M1 Northbound between Sports Drive and the Gateway Motorway. This is the first package of work within the broader $750 million, 8-kilometre M1 North Upgrade, Stage 2 - Eight Mile Plains to Daisy Hill project.
The works involved widening the northbound lanes to 5 lanes to increase capacity, efficiency and safety, as well as to reduce congestion through this busy location. Other key features included improvements to connecting local roads, bus & shared pathway services, and noise reduction for residents on the western side of the motorway.
The challenges
Due to traffic flow and heavy vehicle loading on the road, coupled with daily and seasonal temperature variations, the road pavement is impacted by higher stresses. This is likely to lead to the development and propagation of reflective cracking in the asphalt concrete layers.
These cracks affect the structural integrity of the pavement and allow the infiltration of moisture, resulting in the deterioration of the pavement. This in turn results in earlier maintenance intervention or deep strength rehabilitation works.
Furthermore, underlying pavement construction joints and heavily bound pavement layers can add to the development and propagation of reflective cracks in the road pavement over the life of the asset.
To ensure the final pavement design would withstand these issues, the design needed to ensure the asset performs as per the design criteria and is robust in reducing maintenance expenditure over the life of the asset.
The selection criteria
The approved TMR pavement design consisted of a deep strength asphalt pavement (DSA) for heavy-duty applications. This incorporated an asphalt reinforcement geosynthetic at varying depths, being either below the asphalt intermediate course or as an interlayer within the EME2 high modulus asphalt base course. Additionally, an asphalt reinforcement geosynthetic was chosen to be incorporated over underlying pavement construction joints.
The TMR’s appointed pavement design engineer reviewed technical and performance information on available geosynthetics products in the market to suggest the most suitable product.
The chosen asphalt reinforcement geosynthetic needed to reduce or inhibit the reflective cracking which is to be expected from both the pavement construction joints and the heavily bound (CTB) subbase. It also needed to extend the fatigue life of the asphalt concrete layers during operation.
It was stipulated that the asphalt reinforcement geosynthetic is to be an approved product meeting the TMR Technical Specification MRTS104 – Retarding Pavement Reflective Cracking Using Asphalt Geosynthetics.
A sustainable solution from Global Synthetics
After reviewing the project details and taking into consideration factors such as:
The history and source of the pavement failures
The proposed pavement design
Configuration of the new road alignment, and
Technical and construction requirements
The Global Synthetics technical team suggested Progrid® Compo GC 50/50 Asphalt Geogrid Composite at roll widths of 1.3 m and 3.9 m wide to cater for the entire project design.
Progrid® Compo GC 50/50 Asphalt Geogrid Composite is a combination of a high strength Polyester (PET) geogrid with a fully stitch-bonded, permanent, lightweight and porous PET fabric backing. This ensures it complies with MRTS104 permanent fabric backing requirements and allows for a better installation, fewer wrinkles, and better intimate bonding contact.
Progrid® Compo GC 50/50 Asphalt Geogrid Composite was then chosen and approved as the most suitable geosynthetic product for this project. This solution provided the best outcome during the project construction phase, as well as for the overall performance of the pavement.
Results
Global Synthetics not only supplied the geosynthetic and installation dispenser, but we also provided complimentary onsite project support during various stages of installation.
This included a pre-start site meeting and site supervision as part of the team to ensure the product was installed correctly. In certain situations, our team was able to tailor the installation procedure to satisfy the construction needs without compromising the product performance.
As part of the pre-start meeting with all stakeholders, Global Synthetics engineers collaborated with the installation contractors to run through the manufacturer's installation guidelines and further discussed the construction sequence in detail.
Some of the key highlights during the product installation and duration of the project construction included:
The product was extremely easy to install flat and achieved a very strong bond with the underlying surface and overlying asphalt layer. This was evident during onsite spring balance testing showing results much greater than the min. 9 kg force required under the MRTS104 specification.
Furthermore, on sections where the product was installed below the 50mm asphalt intermediate course which was left exposed to heavy trafficking for a period greater than 6 months and prior to the final open-graded surfacing to be placed; showed no signs of delamination, cracking or shoving under an 80 km/hr speed limit and where traffic congestion occurred regularly during peak hour times.
Our ability to meet the unique needs of the project including supply and onsite support requests at short notice is a testament to our collaborative approach. Being able to make modifications to the installation dispenser during the project to better suit the site conditions and construction sequences ensured the smooth running of the project.
Overall, the installation of Progrid® Compo GC 50/50 Asphalt Geogrid Composite was successfully completed prior to asphalt concrete placement at the end of each shift, without any delays.
The feedback from construction staff and the clients representatives was that the engineering support and collaboration onsite were exceptional, the product is easy to handle, the installation dispenser was very easy to use and efficient, the product was easy to install with minimum wrinkles, and provided a very good bonding.
Design and engineering support for your project
Global Synthetics supplies a wide range of asphalt geosynthetic products including PET and glass fibre geogrids, geogrid composites, geocomposites, paving fabrics and stress absorbing membrane tapes.
This large range of products provides the opportunity for designers and contractors to select the most suitable product for their application. Visit our website for more information about our different asphalt geosynthetic products.
Choosing the right asphalt reinforcement geosynthetic for your application will depend on a range of factors. For assistance in choosing the right product for your individual project, please contact the specialist engineering team at Global Synthetics.
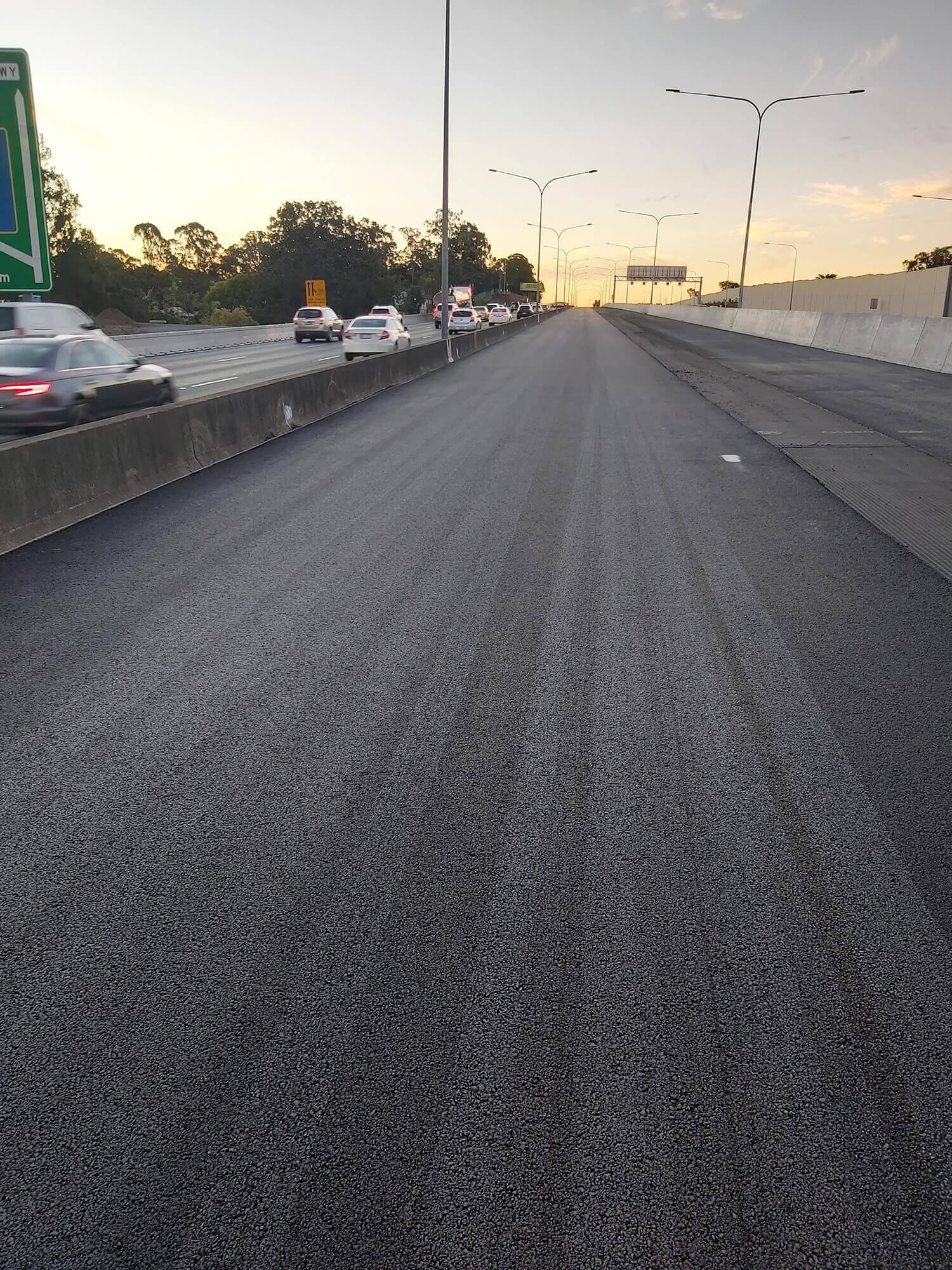
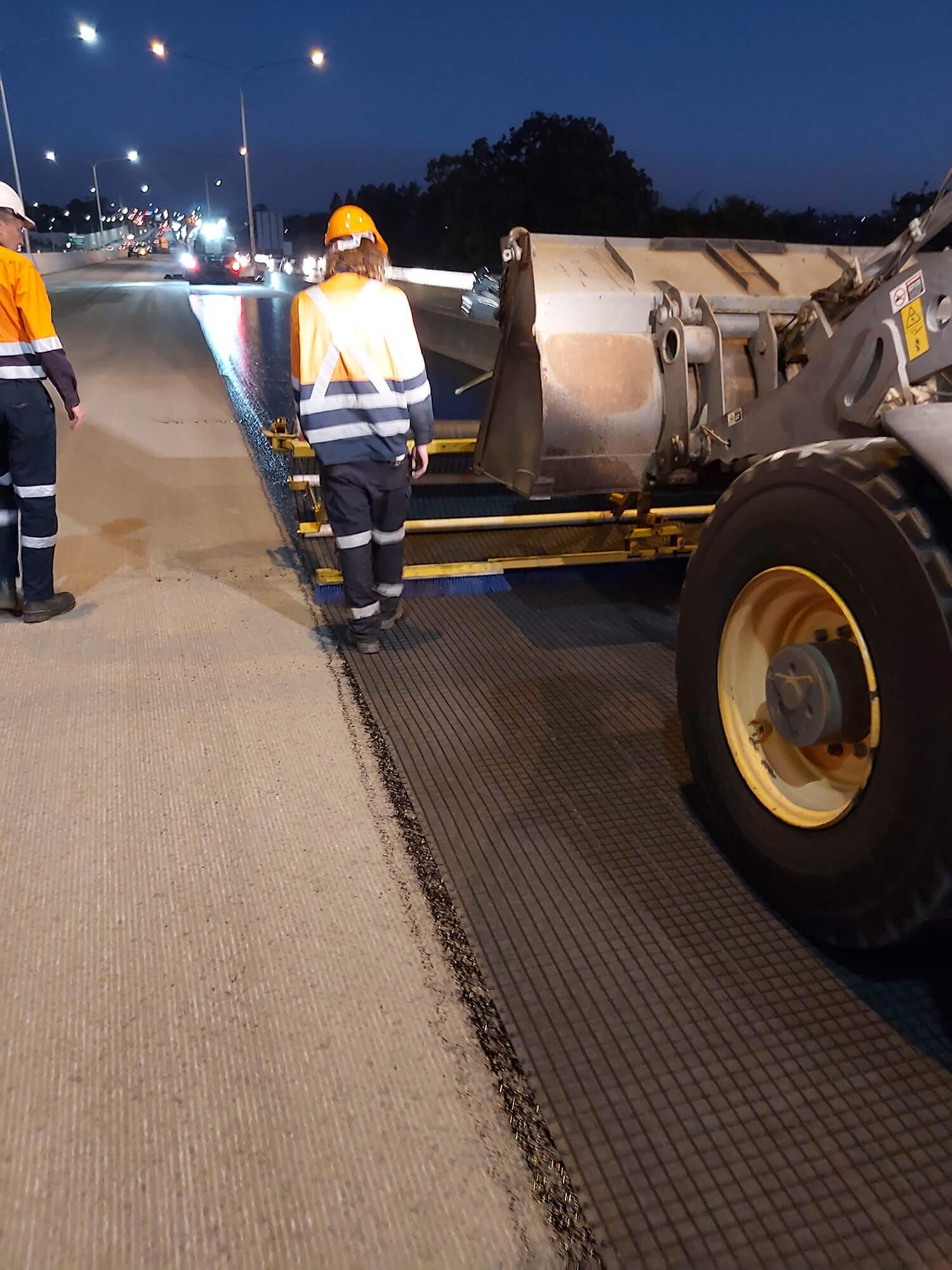
