Case Study: ProTube® Winmalee Dewatering
Location: Winmalee, NSW
Products: ProTube®
General Information
Winmalee Sewage Treatment Plant is a waste water treatment facility located on the western outskirts of Sydney, NSW, Australia. The plant is located in an environmentally sensitive area and is located on an escarpment, near the town of Winmalee, NSW. Site conditions are very constrained with limited space and difficult terrain. The plant is operated by Sydney Water who proposed some extensive modifications within their secondary biosludge reactor basin with additional pump capacity and pipe upgrades required. Prior to such works being undertaken the reactor basin needed to be emptied and sludge removed and transported to disposal.
The Design
A specialist contractor in waste management from Australia was engaged to provide a suitably economic solution to the problems presented by the site location, terrain conditions and environmental restraints. The chosen solution involved the use of ProTube® geotextile dewatering tubes, vacuum truck technology, small amphibious dredging methods and the use of dewatering accelerants.
Two geotextile dewatering tubes were involved in this section of works with a third tube used on the Winmalee site for a different area of work. The tubes supplied were each 13.5 m theoretical circumference and 20m in length. Each geotextile tube has a calculated volume capacity of some 200m3 based on the recommended fill heights for the size of geotextile tube. The geotextile fabric used in the construction of the geotextile tubes was a high strength, high permeability woven geotextile, ACETex GT70/105. The tensile strengths of 105kN/m in the geotextile tube circumference direction and 70kN/m in the axial direction of the geotextile tube. All geotextile tubes were constructed with necessary seams running in the direction of geotextile tube axial direction. Two filling ports were installed in each tube.
Construction
High capacity pumps, for direct delivery of sludge from the basin were used, in combination with a system of vacuum truck tankers discharging into skip bins and then being pumped into the geotextile tubes. Pumps were capable of delivering some 175 liters of sludge per second via 150 mm pipe systems at a potential delivery pressure of some 300 kPa. It took less than 30 minutes to fill one tube using these pumps. The second geotextile tube did use a cationic polymer to assist in dewatering rates. The polymer was supplied in a concentrate liquid form. A preparation mix of polymer was made by diluting 1 part concentrate to 1000 parts of water. This preparation mix was then introduced to the waste stream at a further reduced dilution rate of 10ppm.
In total some 420m3 of sludge in a transportable state was recovered through the use of the geotextile tube process. An additional 250 m3 of sludge was captured in polymer treated settling tanks. A result of a very rigorous maintenance program of daily cleaning of the outer geotextile tube surfaces to limit algal and slime growth which can reduces fabric flow rate.
Performance
The initial geotextile tube supplied did not use polymer accelerants in the dewatering process. Excellent dewatering rates were achieved with full geotextile tube completion obtained within an eight week period. The rate of dewatering was doubled when using the polymer accelerant. The final condition of the material in the second geotextile tube, after four weeks total fill and consolidation time, with a fifteen fill and dewater cycle, achieved similar densities to the first geotextile tube. A feature of this project was the ability of this contractor to fill the geotextile tubes some 40% greater than a theoretically calculated maximum fill height. Actual fill heights of some 2.2m were achieved compared with a theoretical calculated maximum fill height of 1.6m. A traditional alternate treatment of pumping and cleaning, with transfer of total liquid waste to a suitable waste facility, has been estimated to be in excess of $500,000 cost. The geotextile tube process was less than half of these costs.
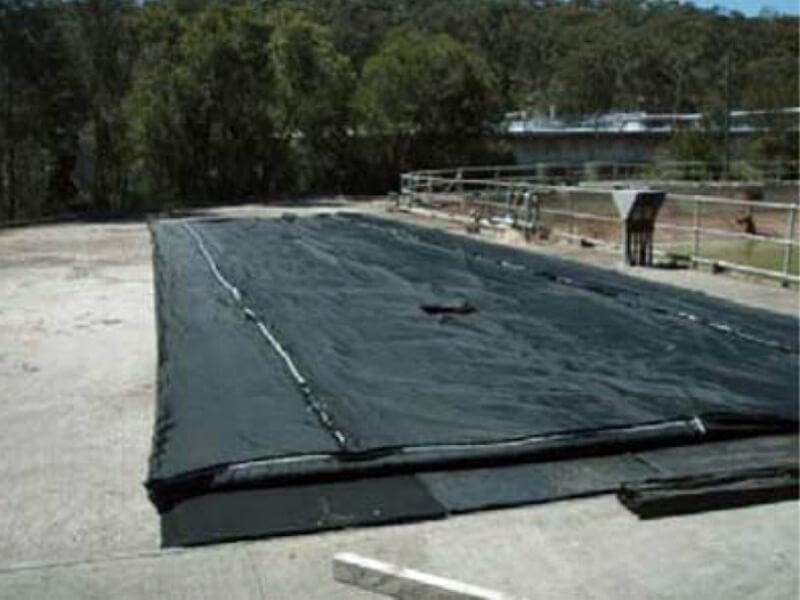
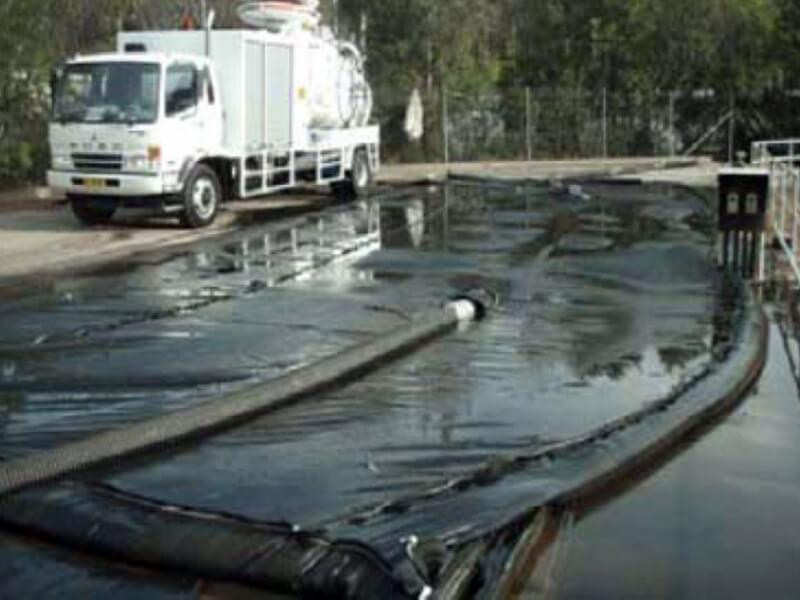
