The Problem
Designing geosynthetics for asphalt overlay resurfacings and rehabilitations is challenging due to the diverse variety of asphalt geosynthetics available in the engineering market. Selecting the right product and suitable bond coat rate is crucial to prevent debonding failure and for enhancing the bonding quality, raising concerns about some products acting as a separation layer.
This technical blog will review the findings of the latest study from an independent international testing project, specifically investigating on the interface shear bond strength and interlocking achieved for all various types of asphalt reinforcement products in direct comparison with each other. The published research paper ‘Optimum tack coat rate for different asphalt geosynthetic interlayers to achieve optimum shear bond strength (N.S. Correia, M.P.S. Silva, A. Shahkolahi (2024))’ is available in the ‘Geotextiles and Geomembrane’ journal.
The intent of this blog is to well inform the engineering industry on the findings of this research and answer the separation concerns raised, specifically relating to the mass of the fabric backing, the presence of fabrics backing after asphalt placement (permanent or temporary), and the amount of bitumen coating content and type of coating on the geosynthetic material. Providing engineering practitioners, the sound knowledge and confidence in the correct selection and installation of a suitable asphalt reinforcement product(s) for this type of application.
The Various Types of Asphalt Geosynthetic Available
Apart from the raw material which can be Polyester (PET), Polypropylene (PP), Polyethylene (PE), Polyvinyl Alcohol yarns (PVA) and Glass Fibre (GS), asphalt geosynthetics can be categorised by type as (1) Paving Nonwoven Geotextiles / Paving Fabrics, (2) Paving Geogrids, (3) Paving Geogrid Composites (Paving Geogrid with a lightweight porous fabric backing), (4) Paving Geocomposites (Paving Geogrid + Paving Nonwoven Geotextile / Paving Fabric), and (5) Geogrid Reinforced Paving Nonwoven Geotextiles / Paving Fabrics (Figure 1).
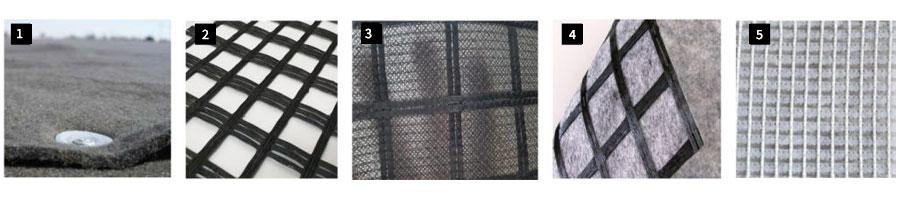
Figure 1 – Example of Different Types of Asphalt Geosynthetic Products
Paving Nonwoven Geotextiles / Paving Fabrics (such as Global Synthetics, ProPave® & ProPave® Enviro (Recycled)) are nonwoven, needle-punched geotextiles which provides stress relief and interlayer barrier functions. Paving Geogrids are open structure products with a high modulus to provide a reinforcement function.
Paving Geogrids (such as Global Synthetics, ProGrid® GBS & ProGrid® GB) are open structure products with high modulus (high tensile strength at low elongation). The grid provides a high tensile strength element within the asphalt producing a composite layer. The idea is to mobilise the tensile strength characteristics of the geogrid with only limited deformation of the pavement. The inclusion of geogrid reinforcement has been shown to effectively eliminate reflection cracking overlays. In asphalt pavements, geogrid reinforcement can also improve the fatigue performance of asphalt layers and can reduce the permanent strains that result in surface rutting.
Paving Geogrid Composites (such as Global Synthetics, ProGrid® Compo GC & ProGrid® Compo GB) are geogrids with ultra-lightweight to lightweight fabric backing or strands partially filling the openings. The fabric backing is a very porous open textile and is only present to assist with adhesion during installation and for reducing the wrinkles. The fabric backing can be ultra-light or light and can be made of Polyester (PET) (i.e., approx. 250 °C melting point, which does not melt after placing the hot mix asphalt) or Polypropylene (PP) (i.e., approx. 160°C melting point, which may melt after placing the hot mix asphalt).
Paving Geocomposites (such as Global Synthetics, ProGrid® GCS (PET of Glass Fibre)) as are geogrids with an attached nonwoven geotextile / fabric which provides the benefit of a Paving Geogrid and Paving Fabric at the same time.
Geogrid Reinforced Paving Geotextiles (such as Global Synthetics, ProPave® PETB) are made of a nonwoven geotextile (providing the Paving Fabric functions) with high strength reinforcing cables/yarns (providing the reinforcement function).
More information about different geogrid types and a comprehensive comparison between their performances can be found in the technical paper ‘What is the Right or Wrong Geosynthetic to Control Reflective Cracking of the Asphalt Layer? (A. Shahkolahi, A. Singh)’ presented at the 19TH AfPA International Flexible Pavements Conference (2023).
The Standard Interface Shear Bonding Test & Specimen Preparation
The standard direct shearing test method for asphalt layers (with and without geosynthetic interlayers) is proposed by Leutner (1979). The Leutner Shear Test (Figure 2) is based on a pure shear test method that applies a constant displacement rate of 50 mm/min along the assumed failure plane of two asphaltic layers until failure (maximum shearing force). Guidelines for conducting the Leutner Shear Test on geosynthetic reinforced asphalt samples can be found in ‘FGVS 770 (2013): Technical Note for the application of nonwovens, meshes and composites in asphalt road construction’ published by ‘German Research Society for Roads and Transport’.
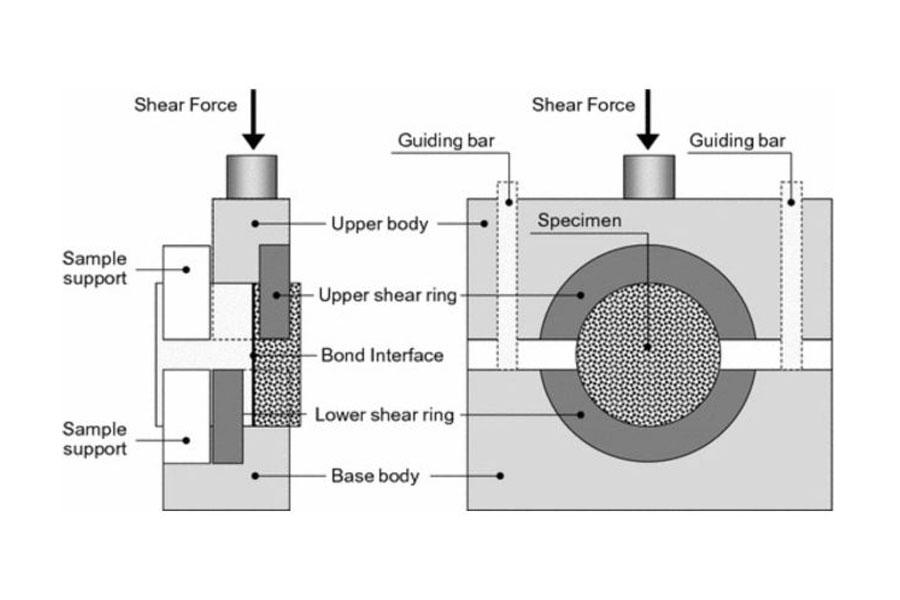
Figure 2 – Schematic of the Leutner Shear Testing Device, (Leutner (1979))
Cylindrical specimens of Hot Mixed Asphalt (HMA) with a diameter of 150 mm; and composed of two asphalt layers and one geosynthetic interlayer are prepared using an adapted/modified Marshall compaction method to conduct interface shear bond tests. Both the lower and upper HMA layers are compacted to achieve a target density of 98%. The amount of pure bitumen bonding coat used for each product was trialled at various indexed rates dependent on each products measured bitumen retention results as well as in accordance with each geosynthetic manufacturers recommendations in their installation guidelines to remove any bias to any one product (Figure 3).
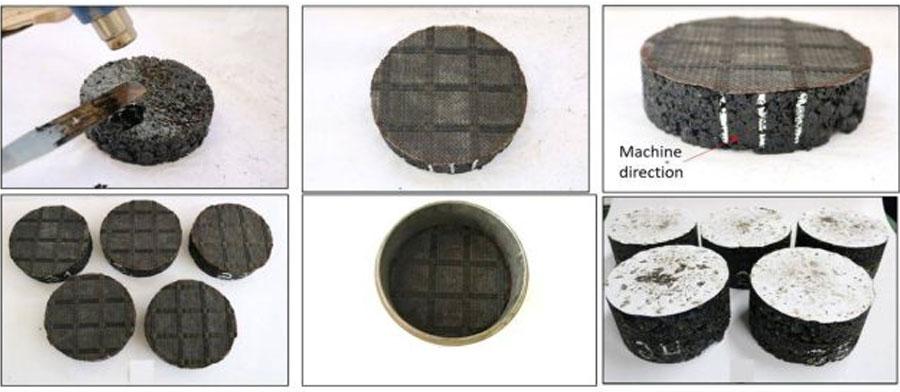
Figure 3 – Specimen Preparation, (N.S. Correia, M.P.S. Silva, A. Shahkolahi (2024)
Tested Products
Excluding a Paving Nonwoven Geotextile / Paving Fabric, all other asphalt geosynthetic types mentioned earlier were tested in the study. The full details of paving geosynthetics used in the study were identified as PaG-1 to PaG-7 (Figure 4).
Geogrid Reinforced Paving Geotextiles – PaG-1 (i.e., Glass Fibre Geogrid and PET Nonwoven Geotextile with no bitumen coating),
Geogrid Reinforced Paving Geotextile – PaG-2 (i.e., PET Geogrid and PET Nonwoven Geotextile with no bitumen coating),
Paving Geocomposite – PaG-3 (i.e., Glass Fibre Geogrid and PET Nonwoven Geotextile with no bitumen coating),
Paving Geogrid Composite – PaG-4 (i.e., PET Geogrid and PET lightweight fabric backing with bitumen coating),
Paving Geogrid Composite – PaG-5 (i.e., Glass Fibre Geogrid and PET lightweight fabric backing with bitumen coating),
Paving Geogrid Composite – PaG-6 (i.e. PET Geogrid with PP ultra-lightweight fabric backing (potentially may melt after asphalt placement) with elastomeric bitumen coating), and
Paving Geogrid – PaG-7 (i.e., Glass Fibre Geogrid with bitumen coating). asphalt paving geosynthetic samples
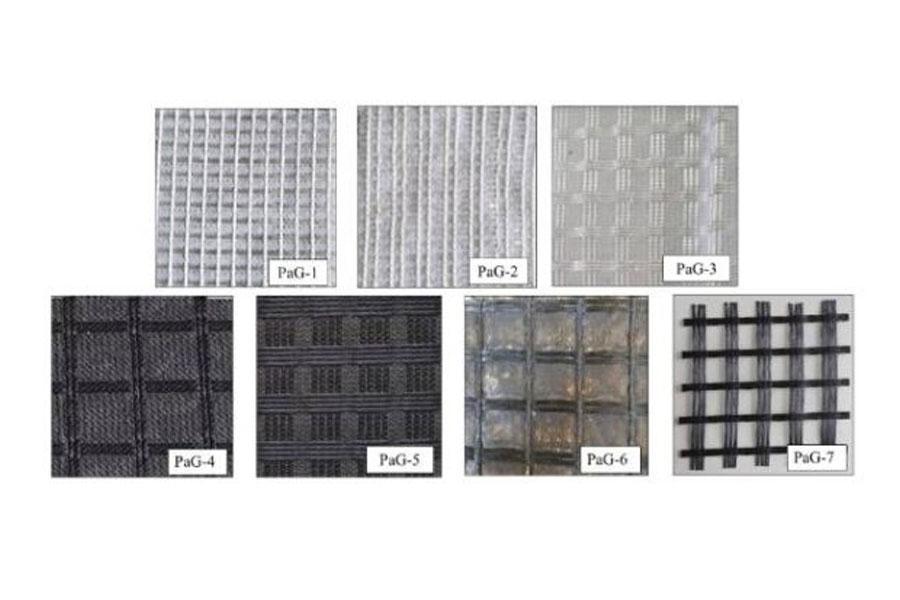
Figure 4 – Asphalt Paving Geosynthetics Used in the Study, (N.S. Correia, M.P.S. Silva, A. Shahkolahi (2024)
The full details of the asphalt geosynthetic material properties (i.e., varying mass, material type and bitumen retention of the fabric backing etc.); various percentage bond coat application rates respective to the specific product bitumen retention; and full study results for interface shear bond strength and interlocking performance can be found in the research paper.
Test Results
All products tested within the study (PaG-1 to PaG-7) with a 100 % application of the pure bitumen bond coat rate to the measured product bitumen retention rate for each product, and regardless of the type and content of existing bitumen coating on the product; all provided above acceptable interface shear bond strength (Figure 5) to the German guideline FGVS 770 (2013) minimum interface shear strength value (i.e., laboratory-prepared specimen corresponding to 0.84 MPa (15 kN))
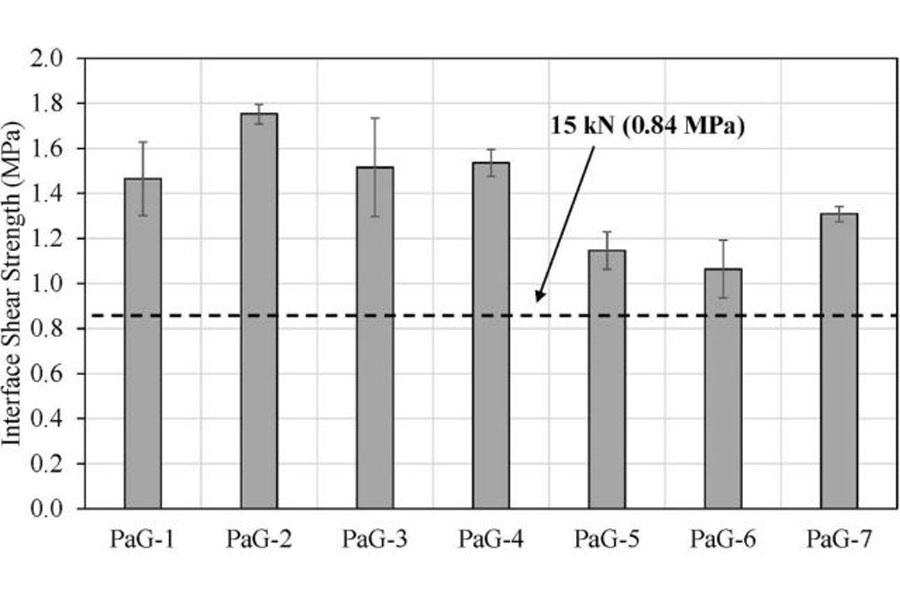
Figure 5 – Interface Shear Bond Strength Results with 100 % Bitumen Retention Rate with a Pure Bitumen, (N.S. Correia, M.P.S. Silva, A. Shahkolahi (2024)
Also observed from post-failure pictures (Figure 6), the interlocking mechanism was evident for the Paving Geogrid (PaG-7) and both the Paving Geogrid Composites specimens (PaG-5 and PaG-4 with permanent PET lightweight fabric backing). It is worth noting, that even with the greater aggregate interlocking observed in the Paving Geogrid (PaG-7) specimen (i.e., geogrid only with no backing) when compared to the Paving Geogrid Composite (PaG-4) specimen (i.e., geogrid with a permanent PET lightweight fabric backing); and according to Figure 5 above, a more superior interface shear bond strength was achieved with the Paving Geogrid Composite PaG-4. Hence, this verifies that the presence of a permanent PET lightweight porous fabric backing will not necessarily eliminate the interlocking between top and bottom aggregates in HMA layers.
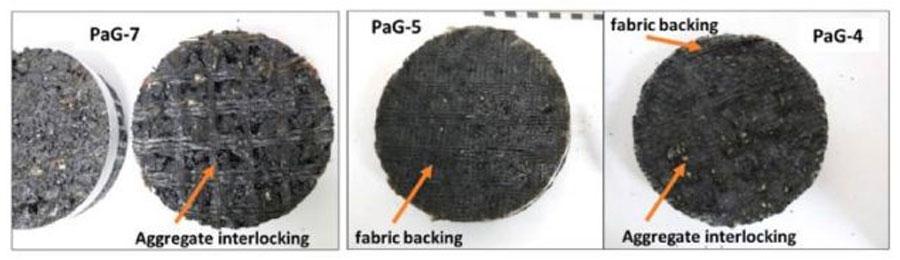
Figure 6 – Post-failure Pictures of Paving Geogrid (PaG-7) and Paving Geogrid Composites (PaG-5 and PaG-4), (N.S. Correia, M.P.S. Silva, A. Shahkolahi (2024)
Learnings & Conclusion
Some of the important learnings about the published paper which scientifically addresses the concerns raised about some products acting as a separation layer:
The developed relationship for bonding/shear strength includes all important and relevant parameters for shear bond strength, in one single parameter. That is another reason this is an important finding. So instead of having a different bond rate value for different products which can change each time from manufacturer to manufacturer, product type to product type, and even product to product grade and properties and fabric backing etc., this unique relation and correlation can be used for all products regardless of the type and properties; and gives a value that includes all the effective properties at the same time.
Different products including PET products, PP products, very light fabric backing, light fabric backing, heavy fabric backing, thin geotextiles, thick geotextiles, PET (permanent) fabric backing, PP fabric backing (potentially melts after AC placement), geogrids, geocomposites, etc., have been tested. Results show that the bonding strength and interlocking of top and bottom AC layer is a complex property and is not dependant on the geotextile mass, type, grading, coating type and amount, etc., individually. It is a mix of all these together, and the lighter or heavier fabric backing, or permanent or temporary fabric backing, and coating type or bitumen content will not reduce the bonding between AC layers if the installation guide and right bond coat rate is followed specific to each product requirement.
In conclusion, the interlocking (where applicable) and acceptable interface shear bond strength for all products can be achieved successfully if the correct bond coat rate is applied; and the interface shear bond is a complex property and is not necessarily / solely and individually related to:
The fabric backing being either permanent or temporary,
The mass of the fabric backing, and
The geosynthetic coating type or bitumen content
The most important aspects being:
To ensure a successful installation outcome (i.e., achieving a strong shear bond and applicable interlocking) for all available products, the manufacturers installation guidelines specific to each asphalt reinforcement geosynthetic product must be always followed; and
To ensure the reinforcement performance benefits for the retardation of reflective cracking, it can be achieved by selecting all products complying to Qld TMR, MRTS104 specification.
For assistance in choosing the right product for your individual project, contact the specialist engineering team at Global Synthetics.
For further information, please contact our National Technical Manager, Amir Shahkolahi (amir@globalsynthetics.com.au) or Technical Business Development Manager – Pavements, Amar Singh (amar.singh@globalsynthetics.com.au)
