What is the problem?
Due to increasing traffic flow and heavy vehicle loading on the road coupled with daily and seasonal temperature variations, the road pavement is impacted by higher stresses leading to the development and propagation of reflective cracking in the asphalt concrete layers. These cracks will begin to affect the structural integrity of the pavement and also allow the infiltration of moisture resulting in the deterioration of the pavement, bringing forward earlier maintenance intervention or deep strength rehabilitation works.
These types of pavement treatment activities are not only expensive for the asset owner but also causes major disruption to the community and road users. Using innovative technological solutions in the road building materials is one way to help improve and extend the asset life and to delay these treatments. When constructing new asphalt concrete pavements and/or asphalt concrete overlays, consideration needs to be given to delaying the onset and propagation of reflective cracking.
Understanding the cause of cracking in pavements
In order to determine a suitable solution, it is first of all necessary to understand the way in which the reflective cracks in road pavements initiate and propagate.
Pavement investigations have identified three (3) modes of cracking being due to Tension, In-Plane Shear and Out-Of-Plane Shear (Figure 1). For example, reflecting cracking can be the result of mode I, mode II, or a combination of mode I and II. It is also important to keep in mind that cracks do not necessarily grow with a constant rate throughout the entire cross-section of the pavement. The type of loading and movements on the pavement layers including insufficient material compaction also influences a variation in the rate of propagation.
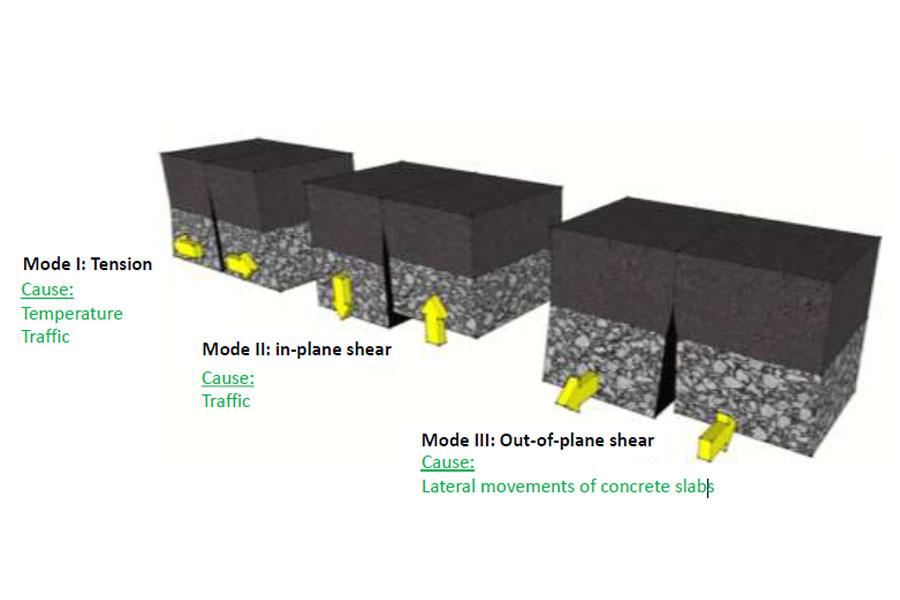
Figure 1. Modes of crack (Nithin et al., 2015) The selection of the most robust raw polymer material such as either Polyester (PET), Glass Fibre, Polyvinyl Alcohol (PVA) and Polypropylene (PP) hinges on the material characteristics such as melting point and load-elongation behaviour, and how they perform under various circumstances. In other words, not all polymers and material characteristics behave or provide the same long term durability and performance outcomes.
What innovative technologies / strategies are available? Various strategies are available for the design and construction of road pavements to control cracking, reducing the infiltration of moisture and increasing the structural behaviour and performance of asphalt concrete overlays. The use of asphalt reinforcement geogrids / geocomposites is one of the solutions for little additional cost which can provide the function(s) of reinforcement (Figure 2), a stress relief layer, interlayer moisture barries or a combination of them to achieve greater benefits leading to considerable cost savings over the life of the pavement asset. A complete definition of these three (3) functions is provided in BS EN15381:2008.
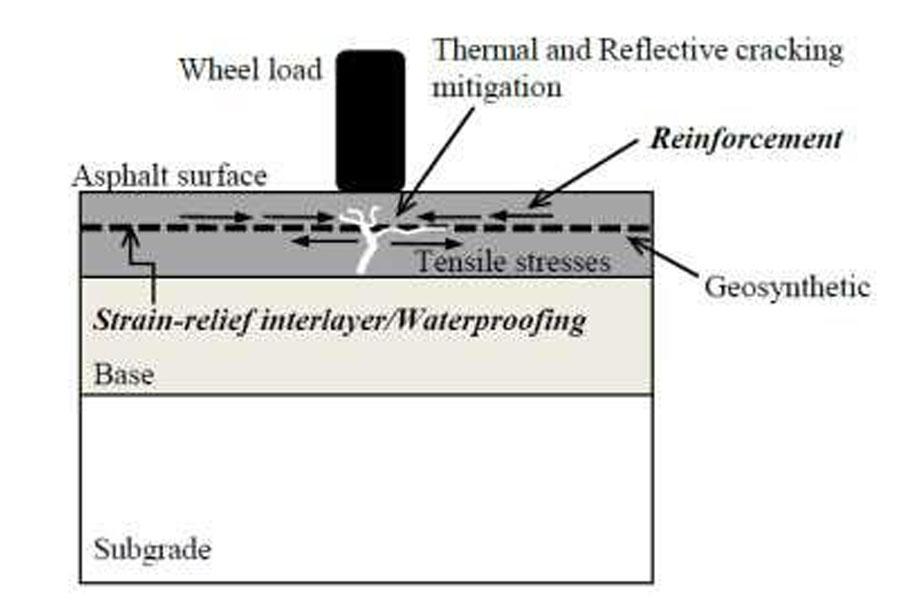
Figure 2. Application of geosynthetics in asphalt overlay (Correia, 2014)
What are the different types of asphalt geosynthetics?
Asphalt geosynthetic products can be categorised into four (4) main categories:
Paving Fabrics: A nonwoven geotextile with minimum mass of 130g/m2 and minimum bitumen retention of 0.9L/m2, installed as saturated with bitumen to provide stress relief layer and/or interlayer moisture barrier.
Geogrids: A synthetic planar structure formed by a regular network of tensile strength elements with apertures to allow for interlocking with the surrounding soil so as to perform the primary function of reinforcement.
Geogrid Reinforcement Composites: A geogrid with an ultra-light (<50g/m2) or light (50-150g/m2) fabric backing. The main function of this product is reinforcement. The fabric backing which is made of temporary or permanent fibre strands partially filling the openings and is purely for better installation and bonding with the tack coat.
Geocomposites: Combination of a geogrid and a paving fabric which gives the benefits of both products and can provide reinforcement, stress relief and waterproofing together.
What are the benefits?
The main function of geosynthetics used in the construction and rehabilitation of roads and pavements subjected to thermal, fatigue and reflective cracking is to reduce the amount of cracking in a new pavement or asphalt overlay. In addition, a stress relief layer and/or a barrier to top-down water ingress into the subbase and/or subgrade may be provided if a geocomposite is used.
Installation considerations
The installation of asphalt reinforcement geosynthetic products is very important in their performance. It is very sensitive to various parameters and can be different for each site, product, weather, surface condition, bonding material, etc. Manufacturers installation guidelines should be followed completely and carefully in all cases.
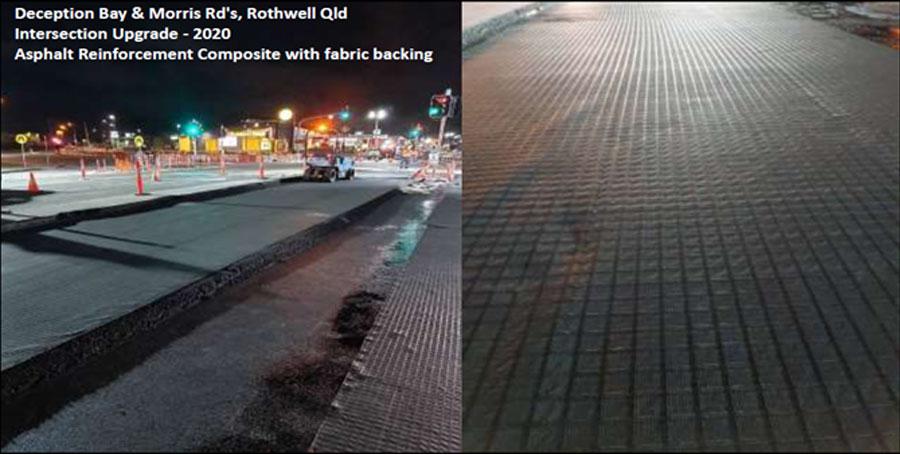
Progrid® Asphalt Reinforcement geogrids / geocomposites
Global Synthetics supplies a wide range of asphalt reinforcement products which provides the opportunity for designers and contractors to select the most suitable product for their application:
Asphalt Geogrids
ProGrid® GC 50/50 and 100/100: Polyester (PET) geogrid.
ProGrid® GB 50/50 and 100/100: Glass Fibre geogrid.
Asphalt Geogrid Reinforcement Composites
ProGrid® Compo GC 50/50 and 100/100: Polyester (PET) geogrid with a PET non-woven light-weight geotextile backing (50 – 150g/m2).
ProGrid® Compo GB 50/50 and 100/100: Glass Fibre geogrid with a PET non-woven light-weight geotextile backing (50 – 150g/m2).
Some key features:
High strength and high temperature resistant.
Increases the fatigue resistance of the asphalt layer, decreases the occurrence rate of reflective cracking under cyclic traffic loads, and extends the service life of pavement.
Bituminous coating and permanent light-weight porous geotextile fabric backing provides better bonding and lesser wrinkles.
Easy to handle and robust against installation damage.
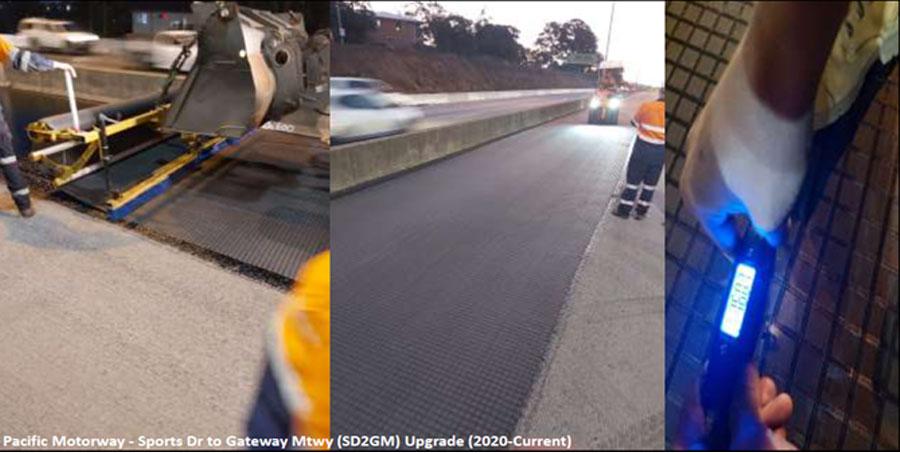
In Summary
It has been found by means of finite element computations, laboratory work and field experience that depending on the factors listed above, a lifetime increase of up to a factor 5 compared to a similar unreinforced overlay can be achieved if a suitable product is installed correctly.
Choosing the right asphalt reinforcement geosynthetics for your application will depend on a range of factors such as:
Existing surface characteristics/condition
Type and severity (movement) of the cracks/joints
Characteristics and nature of the loading and the pavement structure
Location within the overlay
Properties of the material (mechanical, durability, etc.)
Humidity
Temperature
Quality of installation
Compaction of the asphalt layer
For assistance in choosing the right product for your individual project, contact the specialist engineering team at Global Synthetics.
For further information please contact our Business Development Manager – Pavements, Amar Singh (amar.singh@globalsynthetics.com.au) or our Technical Manager Australia & New Zealand, Amir Shahkolahi (amir@globalsynthetics.com.au)
